Chemical activation of fly ash cements
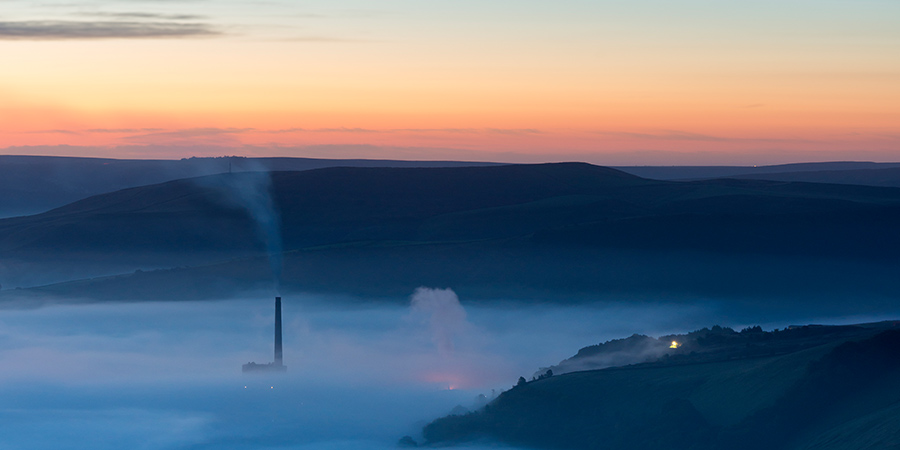
There are many advantages and disadvantages to using fly ash, and cement producers must balance these benefits and limitations. Fly ash helps reduce CO2 emission from cement production. However, when the clinker portion is reduced, the cement typically suffers from lower strength, notably at ages earlier than three days. Since fly ash does not typically begin to react until after seven days, development of an accelerator is desired.
Advantages | Disadvantages |
---|---|
Most abundant supplementary cementitious material (SCM) worldwide (approximately 700 million tpa) | Variable quality and performance |
Pozzolanic activity that contributes to cement hydration | Low early strength and slower setting time |
High fineness and eventual post-mill addition allows for narrower particle size distribution and/or lower kWh/t | High fineness may increase water demand |
Lower mill coating and better cement flowability | Potential for carbon staining |
Allows lower specific CO2 of finished cement | Potential adsorption of admixtures onto carbon |
GCP Applied Technologies (formerly W. R. Grace) created a series of OPTEVA™ ESE® cement additives that enable activation of cement and fly ash hydration, without the use of chloride or thiocyanate. This partially offsets the negative effect of fly ash on cement hydration. This technology frequently leads to superior concrete performance and higher clinker replacement in blended cements by:
- Enhancing the dissolution of the aluminate phases to accelerate the hydration of calcium sulfoaluminate phases
- Changing the amount and morphology of portlandite
- Changing the Ca/Si ratio of C-S-H
- Accelerating the hydration of the fly ash and slag phases
Real-world examples
OPTEVA™ ESE® additives have been used for more than a decade to increase mill output, increase the use of SCMs and allow for the use of poorer grade raw materials, without reducing cement performance.
Case study #1
An OPTEVA™ ESE® additive was successfully applied in the production of fly ash cement, PO 42.5, in a plant in Eastern China. In this case, OPTEVA™ ESE® 100 additive at 250 g/t of cement allowed the plant to increase mill output by 20% at constant fineness, and use 5% more fly ash in the cement while maintaining the same compressive strengths and setting times.
Case study #2
In a similar application in South China, OPTEVA™ ESE® 200 additive was dosed at 300 g/t of PO 42.5 cement, which supported a 5% increase of fly ash compared to blank cement, and a mill output increase of 12%.
Case study #3
An OPTEVA™ ESE® additive was implemented at a European blending plant and used to produce two types of fly ash cement. OPTEVA™ ESE® 300 additive was used at 1,000 g/t to produce CEM II/B-V 42.5N with 27% fly ash while still allowing the plant to comply with stringent strength requirements at all ages. When compared to blank cement, strengths were enhanced from 11 to 13 MPa at one day, from 19 to 23 MPa at two days and from 46 to 50 MPa at 28 days.
The same additive, at 1,500 g/t, was also used to produce a CEM IV/B (V) 32.5R for special applications. In this case, the activation of the fly ash cement allowed for the increase of fly ash content to 45% while still complying with internal and external specifications on setting time and strengths.
Case study #4
OPTEVA™ ESE® 400 additive was adopted at an Indian cement plant that produced PPC cement according to the IS standard, with 34% fly ash. In this application, the OPTEVA™ ESE® additive was able to provide a 12% mill output increase at constant fineness. Clinker replacement was not attempted since the fly ash content was already close to the upper limit allowed by the standard.
More significantly, the OPTEVA™ ESE® additive was able to provide a sufficient chemical activation of the clinker-fly ash system such that it was possible to use different grades of fly ash and clinker in different states of prehydration, especially during the monsoon season. This allowed the plant to maintain a significantly reduced deviation of cement strengths and increase internal compliance from 60 to 80-90%, therefore meeting both internal and external standard requirements while still allowing for the use of variable amounts of lower quality fly ash batches and prehydrated clinker.
OPTEVA™ ESE® additive for fly ash cements, case studies | ||||||
---|---|---|---|---|---|---|
Additive | Cement type | Country | Mill output | Early strengths | Late strengths | Application |
OPTEVA™ ESE® 100 @ 250 g/t | PO 42.5 | East China | From 71 to 85 tph (+20%) | Same | Same | Increased fly ash 5% |
OPTEVA™ ESE® 200 @ 300 g/t | PO 42.5 | South China | From 160 to 180 tph (+12%) | Same | Same | Increased fly ash 5% |
OPTEVA™ ESE® 300 @1,000 g/t | CEM II/B-v | EU | N/A (blending station) | +2 Mpa at 1 day (+18%) and +4 Mpa at 2 days (+21%) | +4 MPa at 28 days (+9%) | Complied with internal quality specifications |
OPTEVA™ ESE® 300 @ 1,500 g/t | CEM IV/B (V) | EU | N/A (blending station) | Same | Same | Increased fly ash, produced specially cement |
OPTEVA™ ESE® 400 @ 500 g/t | PPC | India | From 150 to 168 tph (+12%) | +3 MPa at 1 day | +4 MPa at 28 days | Offset variable fly ash quality and clinker pre-hydration |
Benefits of OPTEVA™ ESE® additive
The chemical activation of OPTEVA™ ESE® additive allows for different possible uses of the additive, such as:
- Increasing the percentage of fly ash (lowering the percentage of clinker) without sacrificing cement performance
- Reducing the cost per MPa
- Increasing cement strength to comply with specifications
- Producing special cements for high-value niche applications
- Mitigating the effects of variable fly ash quality and variable activity of clinkers in different states of prehydration on cement performance
Tags
- Cement production
- OPTEVA™