Identifying and resolving mill ventilation shortfalls
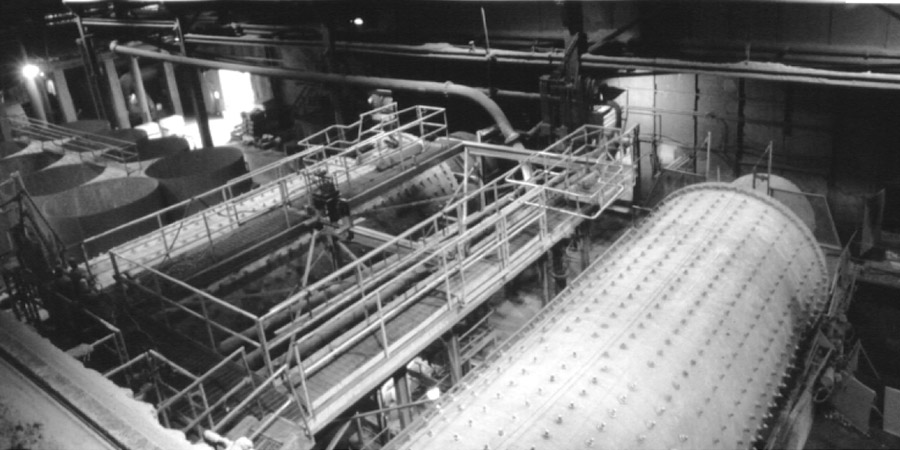
There is a common misunderstanding that to make a finer cement you should reduce the mill ventilation to keep the cement in the mill longer. In fact, this simply leads to over-grinding and increased void filling, which reduces grinding efficiency and often leads to a wider particle side distribution, increased separator rejects and eventual reduced mill output.
To make a finer cement you should speed up the separator. That is what it is designed to do – separate coarse and fine cement. If the separator runs faster, it rejects more (coarser) material back to the mill, leading to a finer finished product. In old open circuit mills this is not possible so the only option is to reduce the mill feed. Open circuit mills are not good at making fine cements.
This is why it’s important to assess the mill ventilation and to know where false air is occurring. False air can enter the system through many routes. The most common is the mill outlet seal. This is usually a soft felt or rubber seal that seals the gap between the rotating mill shell and the static outlet housing. If the seal is covered in hard cement dust, this is often an indication that the seal has not been maintained for some time. The seal gap should be no more than 1mm, but is often larger than this. Replacing the seal and maintaining it in a regular way is necessary to avoid excessive false air.
If the seal is covered in hard cement dust, this is often an indication that the seal has not been maintained for some time.
In this photo, we can see that the felt seal appears in good condition, but it is possible to push a 2-3mm thick safety tag (circled) through the gap. Ideally the gap should be less than 1mm.
Other possible entry points for false air are poorly sealed inspection hatches/doors and routine sampling points. It is not uncommon for QC operators to leave a sample point open to prevent it from blocking. This is fine for the quality team but not so good for mill efficiency. Another common fault is poor sealing around the water injection lance. All these points may seem relatively unimportant, but collectively they can add up to a considerable amount of false air ingress to what should be a sealed system. Hence, it is important to monitor and maintain all possible sources of in-leak, so that the mill ventilation fan pulls as much air as possible through the mill itself.
On older mills, it may also be possible to increase mill ventilation by “opening” the mill inlet, for example by the installation of step-chute feeders.
Good mill ventilation is a primary means of mill cooling and is especially important where high levels of water injection are used.
Tags
- Cement production
- OPTEVA™