Sticky concrete: A growing concern
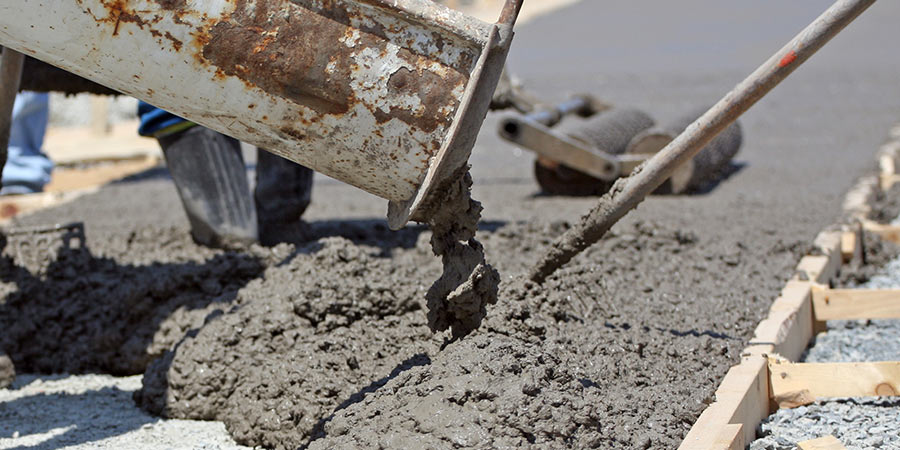
If you’re like most concrete producers, you’re seeing a growing number of issues with sticky concrete. The mix is difficult to discharge and demould, placing an extra burden on plant staff and equipment.
What is sticky concrete?
There is no industry definition for sticky concrete, but it is generally known as concrete that is too heavy, lumpy and tough to work with.
What causes concrete to be sticky?
If there’s not enough water in the mix, concrete will become less workable. What’s important is the ratio of water in the mix, not simply the volume of water. Unfortunately, adding more water won’t fix this problem, since this is likely to degrade the concrete’s strength and cause the mix to segregate.
What is driving the increase in sticky concrete?
There are a number of trends that are causing concrete mixes to be less workable.
- As more of our natural resources become depleted, there’s an increased reliance on using supplementary cementitious or waste stream materials such as recycled aggregate dust, silica fume, slag and other pozzolanic materials in concrete mixes. However, these supplementary cementitious materials are more prone to develop stickiness.
- Poor quality aggregates play a similar role. For example, aggregates that are irregularly shaped or have poor grading result in more friction in the mix, and ultimately are more difficult to move and place. Aggregates with too much clay will hold in water, impacting the consistency of the mix. Aggregates that are too fine also absorb water, commonly resulting in a mix that is more difficult to pour and pump.
- There is an increased market demand for high strength and ultra-high strength concrete for high rises and other major structures. However, a low water-to-cementitious ratio is needed to produce concrete with this high a compressive strength (100-120Mpa+), and this often results in a less workable mix. This can be difficult if not impossible to pump for high rise construction, resulting in costly batch rejects and scheduling delays.
How can you prevent sticky concrete?
There are a few approaches to helping prevent workability issues in concrete mixes.
- New concrete admixtures are available that reduce plastic viscosity or dynamic viscosity and improve rheology. These new polycarboxylate technologies improve workability in ready mix and precast concrete, without the need to add water and potentially degrade the concrete strength.
- Switching raw materials can also have a considerable impact on concrete mix consistency. Using regular shaped aggregates and aggregates with good grading can help minimise stickiness.
- Work with partners with expertise in customising admixtures and mix designs for your specific application, plant and project needs.
What are the benefits of preventing sticky concrete?
Improving concrete workability can result in greater operational efficiency. More workable concrete is easier to produce at the plant, faster to discharge and less likely to stick to the mixing drum. This is also beneficial for concrete contractors, who save labour costs by having concrete that’s easier to pump, place and finish.
Learn more about improving concrete workability with ADVA® LS and MIRA® LS admixtures
Tags
- ADVA Cast
- ADVA®
- Commercial buildings
- Concrete
- MIRA®