Protecting a high-traffic bridge
Built over the Vistula River between 1977 and 1981, the General Stefan Rowecki Bridge, or the “Grota Bridge,” as it is often called, is the second largest in Warsaw, Poland. It is also the busiest bridge in the capital, carrying an estimated 150,000 cars daily.
Refurbishment with minimal disruption
The high volume of traffic and the fact that the bridge forms part of Trasa Torunska - a major expressway through Warsaw - meant that repair and reconstruction work had to be carried out with minimal disruption to traffic flow.
The bridge wasn’t equipped to handle the increasing amount of road users. The original design was made up of a steel orthotropic deck, consisting of two structurally independent parts, each with four traffic lanes. As such, pedestrians and cyclists were restricted to two very narrow tracts, each separated from the roadway by traffic barriers, which made the bridge inaccessible to many people.
Given the time limitations on the construction work and the nature of the structure, the selected bridge deck waterproofing system needed to not only provide proven long lasting protection, but also allow quick and easy application. Most importantly, it needed to have minimal environmental impact over its lifetime.
Once the Grota’s deck was exposed, the project team discovered that it had many irregularities, including protrusions from the steel mesh that could not be removed. The result was that it had an uneven surface profile.
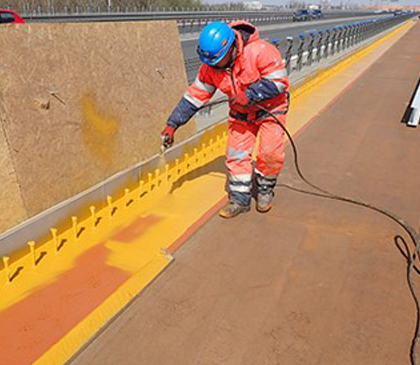
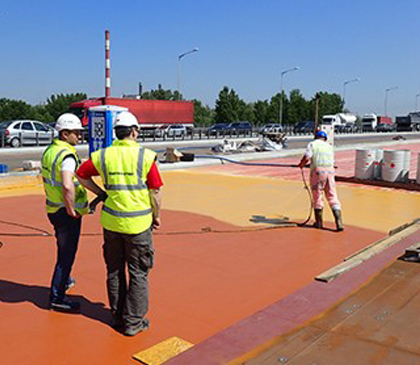
Applying waterproofing under a tight schedule
B7 and ZBM Inwestor Zastępczy Sp. Z o.o. selected the ELIMINATOR® system from Stirling Lloyd (now GCP Applied Technologies). DWD Service Sp. z o.o. prepared the deck by shot blasting using metallic grit, an independent assessment was completed to ensure the correct deck preparation to achieve a strong bond between the substrate and subsequent waterproofing .
The waterproofing system comprised of an initial anti-corrosive primer, ZED S94, which served to protect the newly exposed steel deck and enhance the bond between the deck and membrane. Once this dried, the ELIMINATOR® system was spray applied in two coats of contrasting colours to aid in quality control.
Tack Coat No. 2 was then applied to the membrane, an adhesive that helps to enhance and ensure a strong bond between the membrane and the surfacing. The adhesion between the deck, the ELIMINATOR® system and surfacing was crucial for extending the life of both the surfacing and the structure.
Due to the fast curing and the ease of application of the ELIMINATOR® system, DWD were able to apply 1000m2 of the full bridge deck waterproofing system per day.
Blue360sm Total Business Advantage.
The power of GCP products, performance and people
th.gcpat.com | Thailand customer service: 66 2 030 9700
GCP Applied Technologies Inc., 2325 Lakeview Parkway, Alpharetta, GA 30009, USA
GCP Applied Technologies Holdings (Thailand) Limited., 848 Moo 2, Bangpoo Industrial Estate (North), Phraksa Mai, Muang Samutprakarn, Samutprakarn 10280, Thailand
This document is only current as of the last updated date stated below and is valid only for use in Thailand. It is important that you always refer to the currently available information at the URL below to provide the most current product information at the time of use. Additional literature such as Contractor Manuals, Technical Bulletins, Detail Drawings and detailing recommendations and other relevant documents are also available on www.th.gcpat.com. Information found on other websites must not be relied upon, as they may not be up-to-date or applicable to the conditions in your location and we do not accept any responsibility for their content. If there are any conflicts or if you need more information, please contact GCP Customer Service.
Last Updated: 2025-05-19
https://th.gcpat.com/en-gb/inspiration/project-profiles/eliminator-overcomes-tough-environmental-challenges