Reducing concrete cracking
Top 10 tips for achieving high-quality concrete
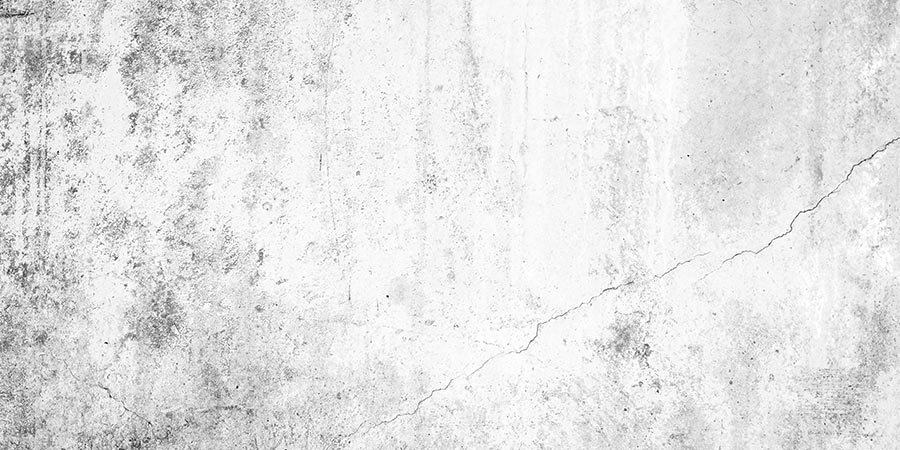
Concrete cracks can be nerve-wracking to deal with, impacting not only the aesthetics, but also the structural integrity of a building. There’s no way to completely eradicate cracks, but here are 10 ways to minimise these bothersome defects.
1. Keep an eye on the temperature. Cracking can occur due to large temperate differences between the concrete and the air and/or the surface it’s being placed on. Never place concrete on surfaces that are less than 35° F (or 1.7°C), and be sure that the temperature difference between the concrete and the air should not be greater than 20° F, except when temperatures above 50° F occur for more than half of a 24-hour period. With slab on grade construction, ensure that the subgrade is properly compacted and the slab and subgrade are sloped for proper drainage. In cold weather, be sure any snow or ice is removed before placing the concrete.
2. Prevent excess water. Control measures are needed to prevent differential volume changes in the concrete. High water content in a concrete mix design is one of the primary causes of differential volume changes that cause high shrinkage and excessive cracking. The use of chemical admixtures, such as water reducers, creates easy-to-place, high slump concrete, without adding excess water.
3. Look into using synthetic micro fibers. Settlement cracking can occur due to restraint by reinforcing steel. Using micro fibers can help reinforce concrete to prevent these cracks. By equally distributing micro fibers throughout the concrete, you can improve impact resistance and crack control.
4. Brace formwork. Ensure that the brace formwork can withstand the pressure of the concrete without movement. In addition, general formwork design can reduce cracking (i.e., thin form board between properly spaced braces can still allow for cracking).
5. Use formed joints. Ensure proper control joint spacing for flatwork in addition to walls of any thickness. For contraction joints, for example, use the height of the wall (for walls greater than 12’ tall) and three times the height of the wall (for walls less than 8’ tall). However, control joints should be used for walls of any thickness.
6. Explore pre-curing options. Fogging or the use of surface plastic between finishing operations can mitigate cracking. In severe weather conditions, you may want to reschedule placement.
7. Provide sufficient concrete cover. For concrete that is cast against or is permanently in contact with the ground, the cover should be at least 3 inches.
8. Start curing the concrete as quickly as possible. A longer curing period than is generally required for compressive strength may be needed in cold weather to reduce cracking. Apply a curing compound or protect it with damp burlap or other covering for at least three days. You may then want to add a second coat of curing compound.
9. Cool gradually. The concrete surfaces exposed to cold weather should be gradually cooled at the end of the protection period to protect against surface cracking.
10. Pay special attention to timing of the concrete finishing process. During finishing, initial screeding should be followed immediately by bull floating. Don’t do finishing work when water is on the surface or before concrete has finished bleeding.
Read about GCP’s complete concrete solutions
Tags
- CONCERA®
- Cement production
- Concrete
- Concrete admixtures
- Engineer
- Structural Solutions