Waterproof concrete: Is it enough for protecting foundations?
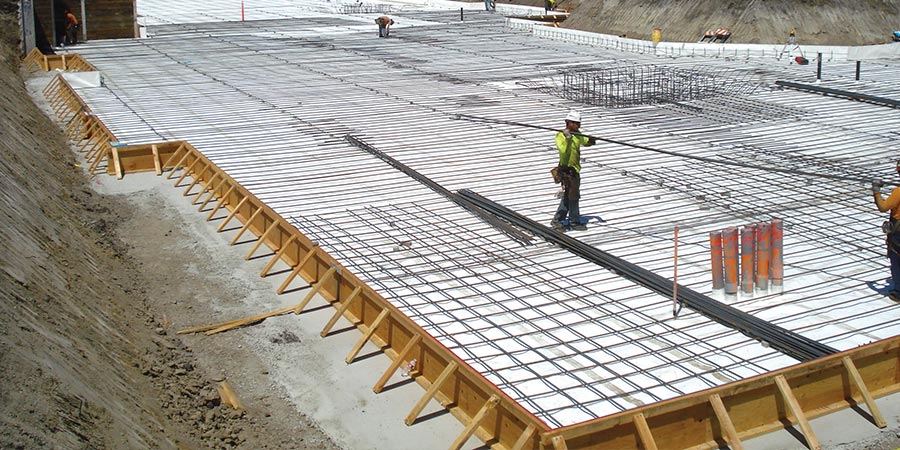
Waterproofing protects your structure and the assets within it against damaging moisture, humidity, and floods. Although waterproofing systems account for a small fraction of the cost of an overall building project, if the wrong solution is chosen or it’s installed improperly, the costs of remediation can be tremendous.
Risk of water ingress
Usually the amount of water used in concrete is much more than is required to hydrate the cement. This excess water takes up space in the concrete, forming a network of capillary voids. This provides channels for water to penetrate the concrete when subjected to hydrostatic pressure or capillary action. The risk of water ingress is even higher when the foundation is being built at or near the water table or in areas where there is heavier soil that’s prone to carry more moisture.
Creating waterproof concrete
Waterproof admixtures are used to create waterproof concrete. The admixtures reduce the chance of water ingress by reducing the permeability and drying shrinkage of concrete.
When to use waterproof concrete
Waterproof concrete (also called integral concrete) is generally best for water retaining structures and less critical basements that are less than 10 meters deep, where soil conditions are not aggressive, and where the consequences of flooding are less severe. This includes unfinished, basic utility spaces such as car parks and workshops where some seepage and damp patches are tolerable.
Advantages and disadvantages of waterproof concrete
Low material costs and ease of application are two advantages of waterproof concrete. To produce waterproof concrete, the ready mix producer incorporates a special admixture into the concrete. The general contractor doesn’t have to worry about allowing time for waterproofing the concrete separately.
However, extra care is needed in the workmanship of concrete placement and finishing as well as the selection of raw materials when you rely on the concrete being waterproofed. Poor casting and vibration, insufficient curing of the concrete, and lower quality aggregates can result in honeycombing, shrinkage cracks, or structure cracks that will allow water to penetrate the structure. In addition, adding water to the mix while the concrete is in transit can compromise the permeability of the concrete. A good concrete mix and proper quality control are important for alleviating these problems, but challenging to meet given project budget and schedule pressures.
Repairing waterproof concrete
All concrete cracks. Shrinkage, temperature-related stresses, and related issues all cause cracking. Even the tiniest crack is a path for water. Waterproof concrete admixtures help to reduce cracks, but they don’t eliminate them.
When waterproof concrete fails, injection grouting is typically used to address it. However, it can be difficult to isolate the source of the leak in these situations since the water can migrate within the concrete slab or concrete walls. This is not only expensive to fix but it can lead to serious problems like mold since there’s no way to actually remove the water once it’s in the concrete. This is another reason why waterproof concrete is best left for low-risk, unfinished spaces, because having to open up walls for injection grouting would be troublesome and expensive. In deep basements in particular, it is difficult if not impossible to gain access to locate and repair leaks.
When waterproofing concrete isn’t enough
For finished spaces that require a dry environment or utility rooms/storage spaces or deep basements that have limited tolerance for water vapor, pre-applied waterproofing membranes are preferable to waterproofing concrete, because they can resist hydrostatic forces that would otherwise push water into the structure. With pre-applied waterproofing, the waterproofing barrier is placed prior to the concrete slab and walls being poured. The concrete is then poured on top of the membrane, forming a bond to keep water and moisture out.
With fully bonded, pre-applied waterproofing, the membrane essentially compensates for structural failures. For example, if gaps form due to ground settlement, the waterproof membrane should remain affixed to the concrete. In addition, any repair issues should be minimal due to the strength of the bond between the concrete and the membrane itself. This bond prevents water from migrating laterally, so if a leak does occur, it’s easier and less expensive to isolate it and fix it than it would be with waterproofing concrete.
Another major advantage of pre-applied membranes like the PREPRUFE® Plus membrane is the protection it provides from harmful gases in the soil. This helps to reduce potential health risks for building inhabitants. This is a major advantage when building in areas where the soil has high amounts of methane or radon, or where there is soil contamination.
Learn more about PREPRUFE® Plus waterproofing membrane
Tags
- Preprufe®
- Waterproofing